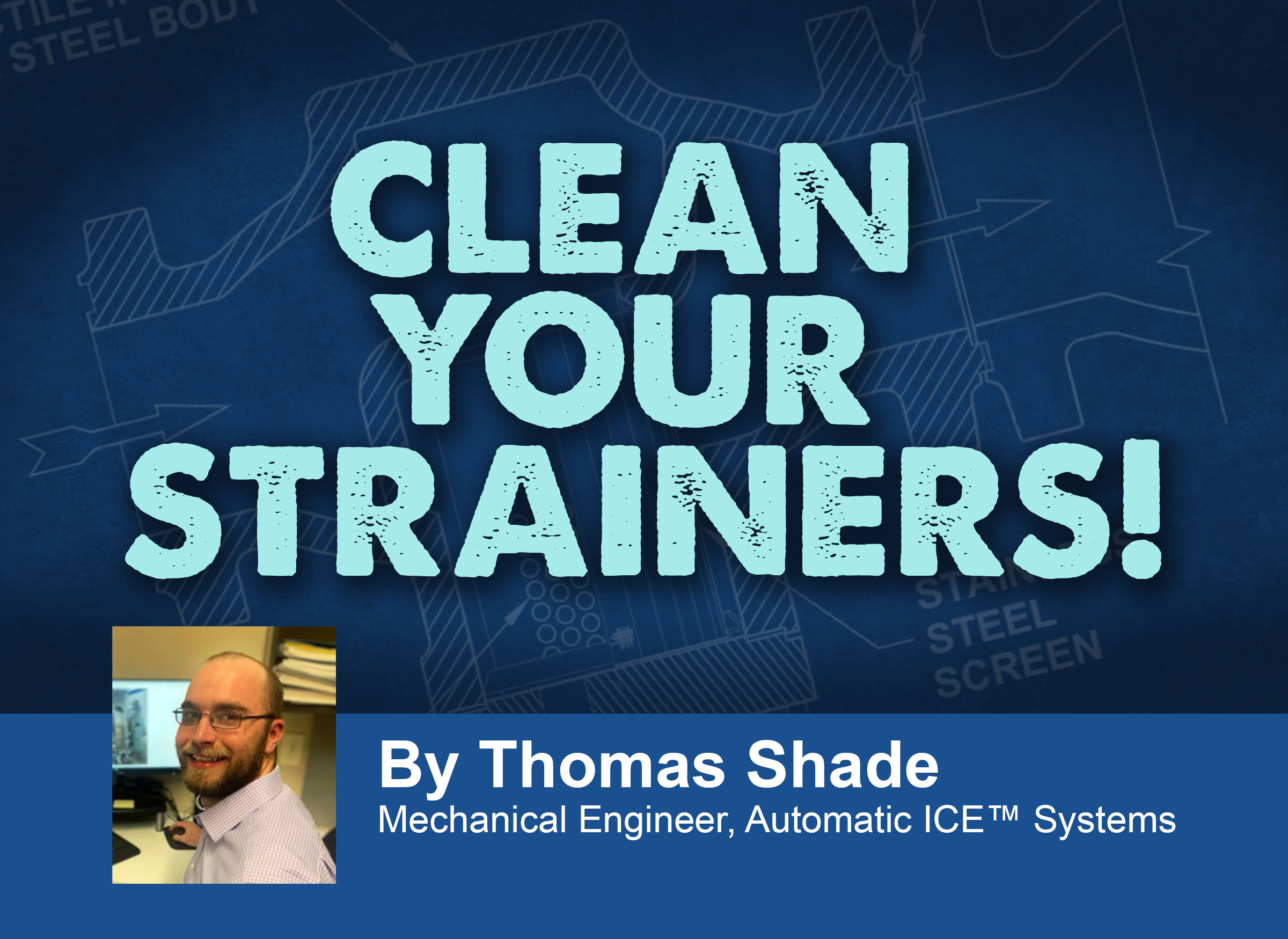
Strainers are installed in every refrigeration system and most plumbing systems. The job of a strainer is to protect pumps, compressors, valves, and equipment from foreign debris, dirt, weld slag, and sediment. They are essentially an in-line filter to catch junk circulating in the system.
Strainers must be cleaned regularly!
Strainers filter out debris that must be removed. When strainers aren’t cleaned, debris builds up and prevents flow. Sometimes, the mesh screens break from the debris and must be replaced.
REFRIGERANT STRAINERS
Refrigerant strainers protect compressors, solenoids, and valves. They are typically installed in-line before solenoids, motorized valves, pumps, and pressure regulators. Compressors also have a suction strainer at the inlet to the compressor.
- Vilter recommends cleaning or replacing the suction strainer every 6 months to 1 year.
- Hansen in-line strainers should be inspected and cleaned at the same interval. They should be checked more frequently on a new system, as they will catch any leftover construction debris.
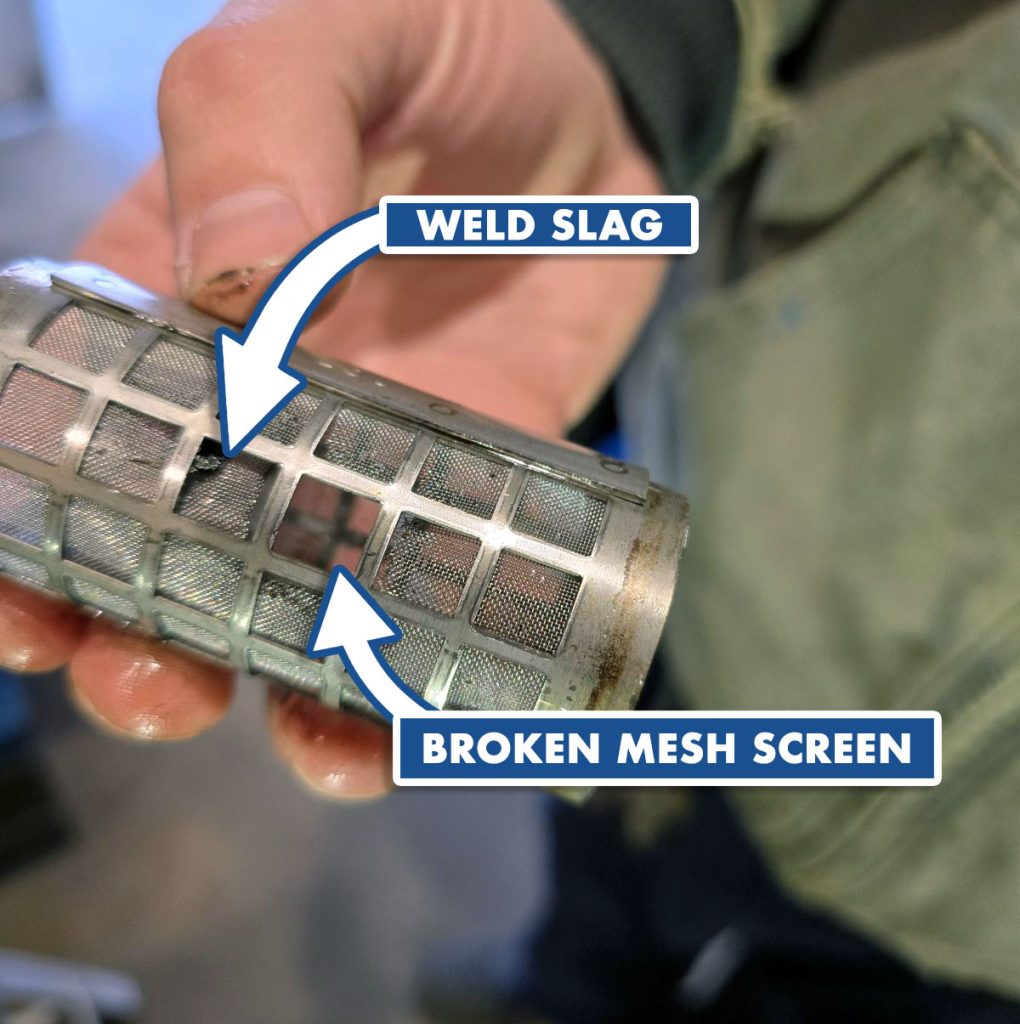
With the valve group pumped out, it is a good time to check and clean the solenoid tube and plunger.
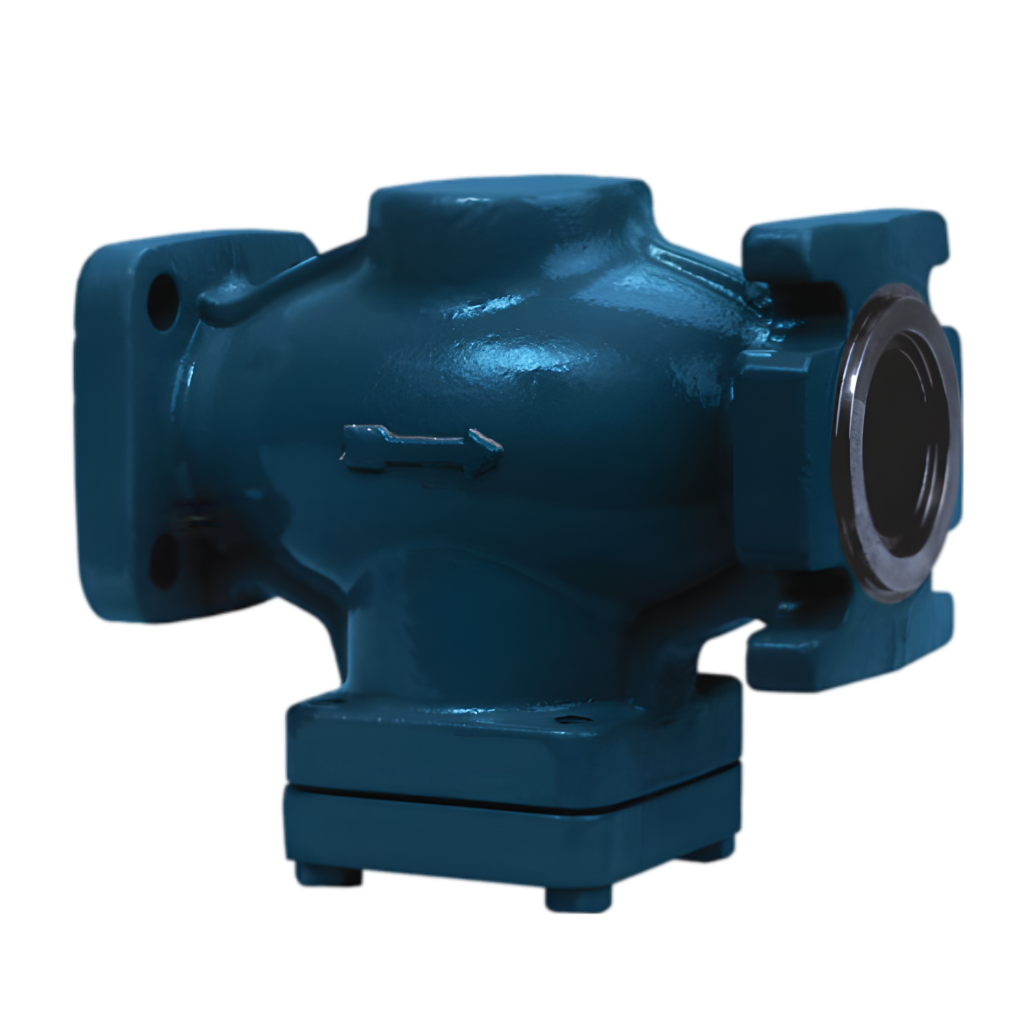
Hansen’s maintenance instructions are below:
Service & Maintenance
Repeated inspection of strainers during system start-up or repairs is essential for optimum benefit. Before opening a strainer, or any other component, be sure it is isolated from the system and all refrigerant is removed (pumped out to zero pressure). The ¾” through 6” strainers have a drain plug in the bottom cover for connecting a drain valve and hose for proper and safe removal of any trapped liquid refrigerant.
Screen Removal and Cleaning: Be careful to avoid any refrigerant which may still be in the strainer. For the ½” strainer, slowly remove the hex bottom cap, then remove the screen assembly. For ¾” through 6” strainers, loosen the bottom cover bolts and bottom cover, check for refrigerant presence, and then remove the bolts, cover, and screen assembly. Clean the screen assembly with a good solvent, blow dry, and inspect. If the screen is damaged or sediment cannot be removed from the screen, replace the screen assembly. Carefully align the screen assembly in the center of the strainer body and replace the bottom cover. Pressure test for leaks before returning to service.
WATER STRAINERS
Strainers are typically installed in most water systems just before the pump. This is especially important in systems with a cooling tower. The cooling tower sits outdoors and circulates a high volume of air and water, which can collect debris, particulates, and other foreign objects. The strainer is the first line of defense in the system.
Dangers of Infrequent Strainer Cleaning
- Pump Damage: If strainers are not cleaned regularly, debris can pass through, causing blockages or wear on the pump impellers. This can lead to pump failure and costly repairs.
- Reduced Efficiency: Clogged strainers restrict the flow of water through the system, causing increased resistance and higher energy consumption to maintain the same performance level.
- System Overheating: Restricted water flow can lead to overheating of the pump and high head pressure on the ice maker, potentially causing failure and even damage to the cooling tower.
- Corrosion: A build-up of sediment can lead to the corrosion of the strainer or pump components.
- System Downtime: If strainers become too clogged and fail, the entire system may need to be shut down for repairs, resulting in expensive downtime and loss of productivity.
The frequency of strainer cleaning depends on several factors, including the quality of the water, the operating conditions, and the size and type of strainer. In general, strainers should be inspected at least every 3-6 months and cleaned more frequently if the water contains higher amounts of debris. In more demanding environments, monthly inspections may be necessary.
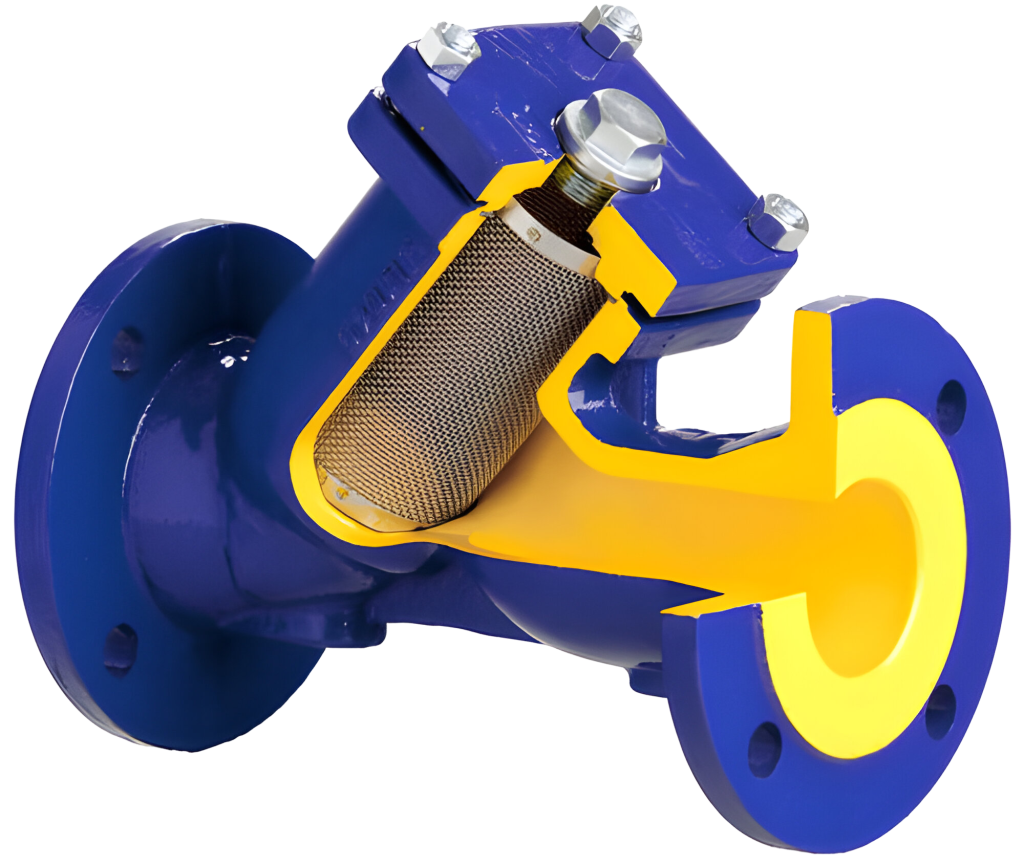
Instructions on how to check and clean water strainers:
- Shut Down the System: Always ensure that the system is powered down and that the pressure has been relieved before beginning any cleaning. Strainers have a plug on the bottom where a valve is typically installed for blowdown.
- Remove the Strainer Cover: Open the strainer housing to access the mesh element.
- Inspect the Strainer: Examine the condition of the strainer for any signs of corrosion, damage, or excessive debris build-up. Check the filter mesh for integrity, as any tears or breaks could allow debris to pass through.
- Clean the Strainer: Use a high-pressure water jet or a soft brush to remove accumulated debris.
- Check for Blockages: Ensure that the strainer’s perforations are clear and that water can flow freely through it.
- Reassemble and Test: Once cleaned, securely replace the strainer cover and restore the system to its operational state. Then, test the system for proper flow and performance.
If your company needs advice on maintenance tips or anything else, AIS can help you make the right decisions to meet your needs today and as your company grows.