When was the last time you had industry professionals perform a site survey done of your facility? If you can’t remember, it is time to schedule one with AIS. Typical site surveys include 1 or 2 personnel traveling to your facility for as little as a half day or as long as a couple of days. We use this time to walk through your system, collect data, record parameters, and identify opportunities for improvement. In today’s world, with ever-increasing costs of water, electricity, equipment, labor, fuel, and about everything else, let us help you find those opportunities to increase capacity and save money. Regular site surveys can reveal numerous opportunities that enhance performance, increase operational reliability, and achieve significant energy savings. Here are just a few of the things we investigate on our site surveys:
Equipment Sizing and Bottleneck Identification
We collect nameplate data and evaluate whether the existing equipment is appropriately sized for the plant’s demands. Identifying and addressing bottlenecks in the system can significantly enhance capacity and reduce energy consumption. Sometimes, simple adjustments, such as resizing or adding controls, can yield substantial benefits with minimal capital expenditure.
Condenser Drain Piping and Liquid Stacking
One common issue is improperly installed condenser drain piping, which can lead to liquid stacking in the condenser. This situation reduces compressor capacity, increases energy usage, and raises the head pressure. During site surveys, we inspect the condenser drain piping and look for signs of improper installation or liquid buildup. Solutions may involve reconfiguring the drain piping or adding equalizer lines from the high-pressure receiver (HPR) to the condenser’s inlet. This adjustment can alleviate liquid stacking and lower head pressure significantly. Another essential item we look for on the condenser piping is purge valves. Non-condensibles like air can get into the system from regular maintenance and significantly reduce condenser capacity. Non-condensibles need to be purged from the system occasionally to ensure optimal performance. If purge valves are not present, we can help create a plan to install those during the next shutdown.
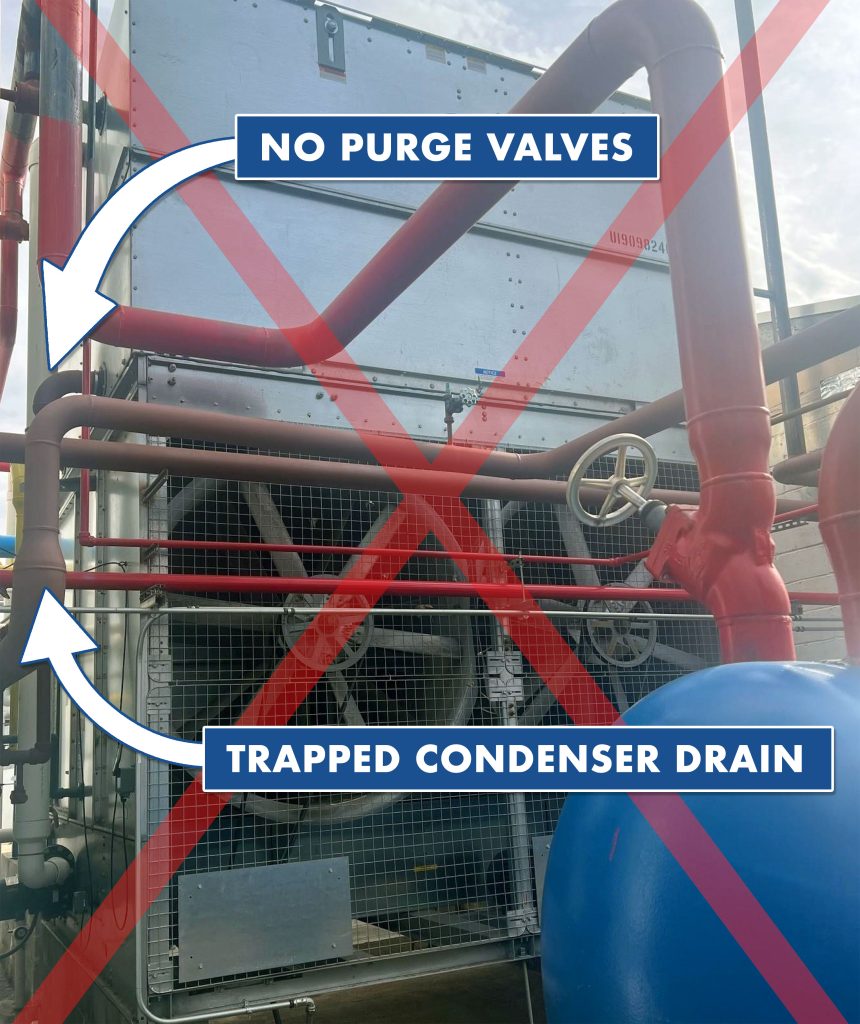
Suction Accumulators and Liquid Carryover
Another frequent problem is undersized suction accumulators. This can lead to liquid carryover issues that can damage the compressors and affect overall efficiency. We assess the existing accumulators’ size and functionality during our surveys. If the accumulator is of adequate size, we often recommend retrofitting them with liquid-level probes, if they don’t already have one. These probes allow the system to shut down or trigger an alarm before the liquid level reaches the high-level cutout, thus preventing liquid carryover and maintaining compressor performance. If the accumulator is undersized, we can help engineer a replacement vessel and upsize it to accommodate any future expansion at little cost.
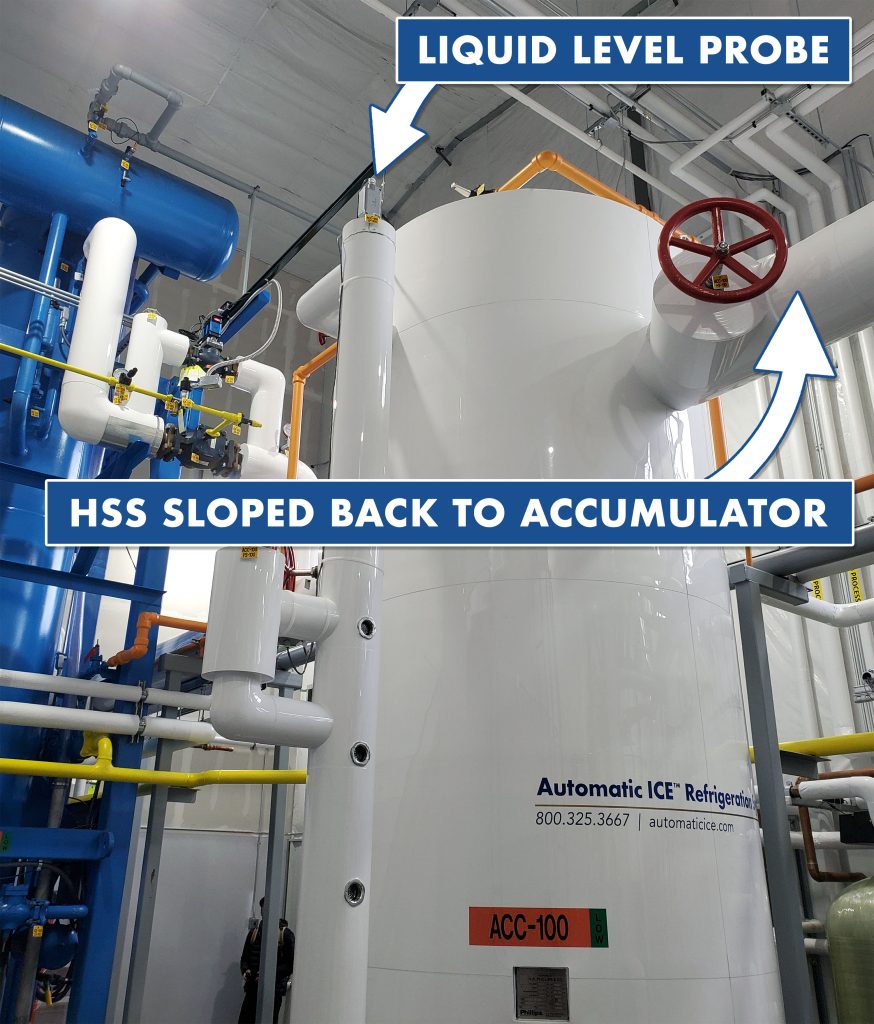
Water Usage and Quality
Efficient water management is crucial for optimal ice production. We assess the water meter and piping to determine if there is adequate pressure and flow. Low flow can lead to many issues, including a significant drop in ice production. We also examine condenser coils for scale buildup, as even a thin layer of scale—about 1/64 inch—can reduce performance by up to 15%. We can suggest different condenser sump setups for adding water treatment systems. Additionally, we offer solutions for water conservation, such as installing solenoids or motorized valves on the Vogt water supply line, ensuring that water does not flow down the drain when the machine is not in operation.
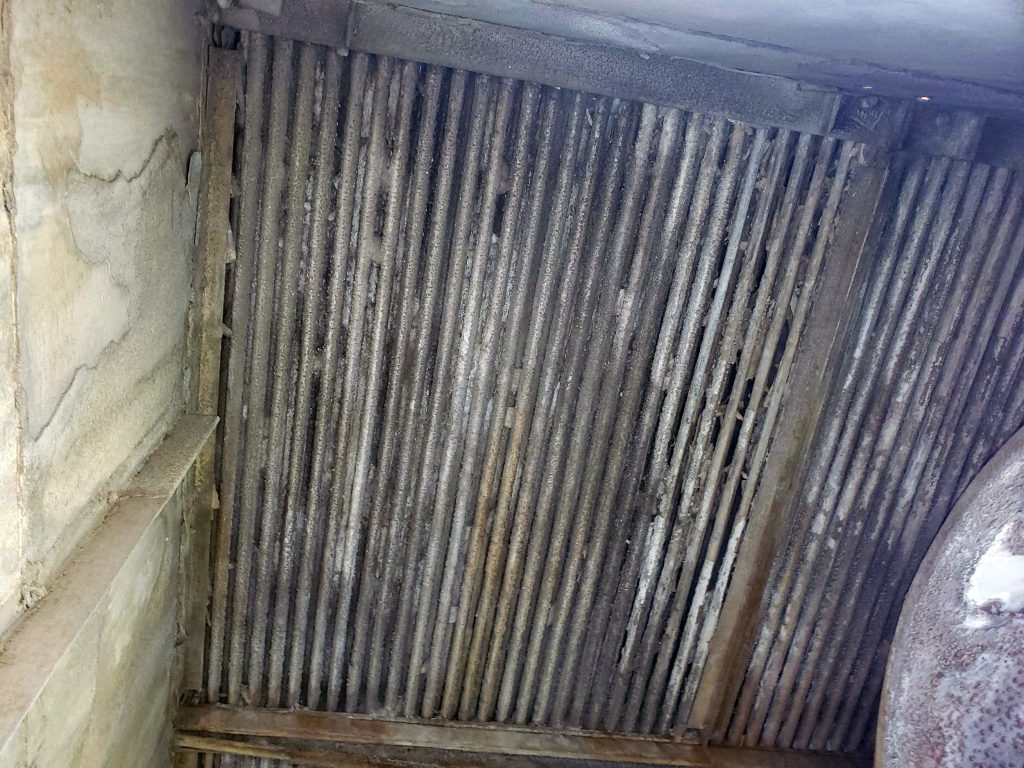
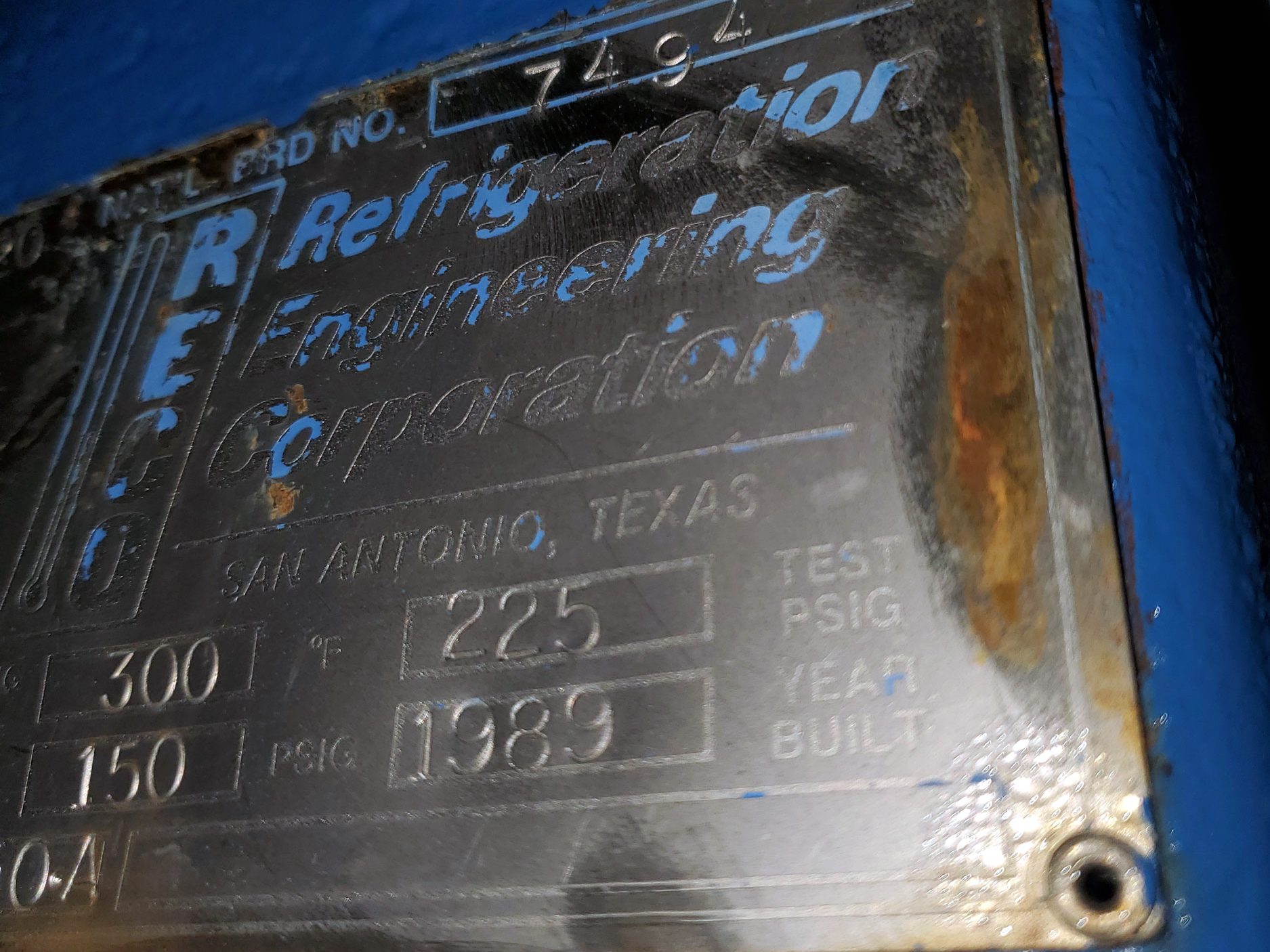
Pipe Sizing and Slope
Improperly sized or sloped piping can lead to unnecessary pressure drops and liquid accumulation in undesirable areas. One common issue we find is a hot gas pipe that is sloped towards the ice maker. When the system is shut down, ammonia condenses in the pipe, which will fill the ice maker with ammonia as soon as it goes into its first harvest. Compressor suction piping is also another common issue. The HSS piping should slope back to the accumulator, and the drop to each compressor should come off the top of the header to ensure no liquid can reach the compressor. Adjustments might include resizing pipes or correcting slopes to prevent liquid buildup and ensure optimal system performance.
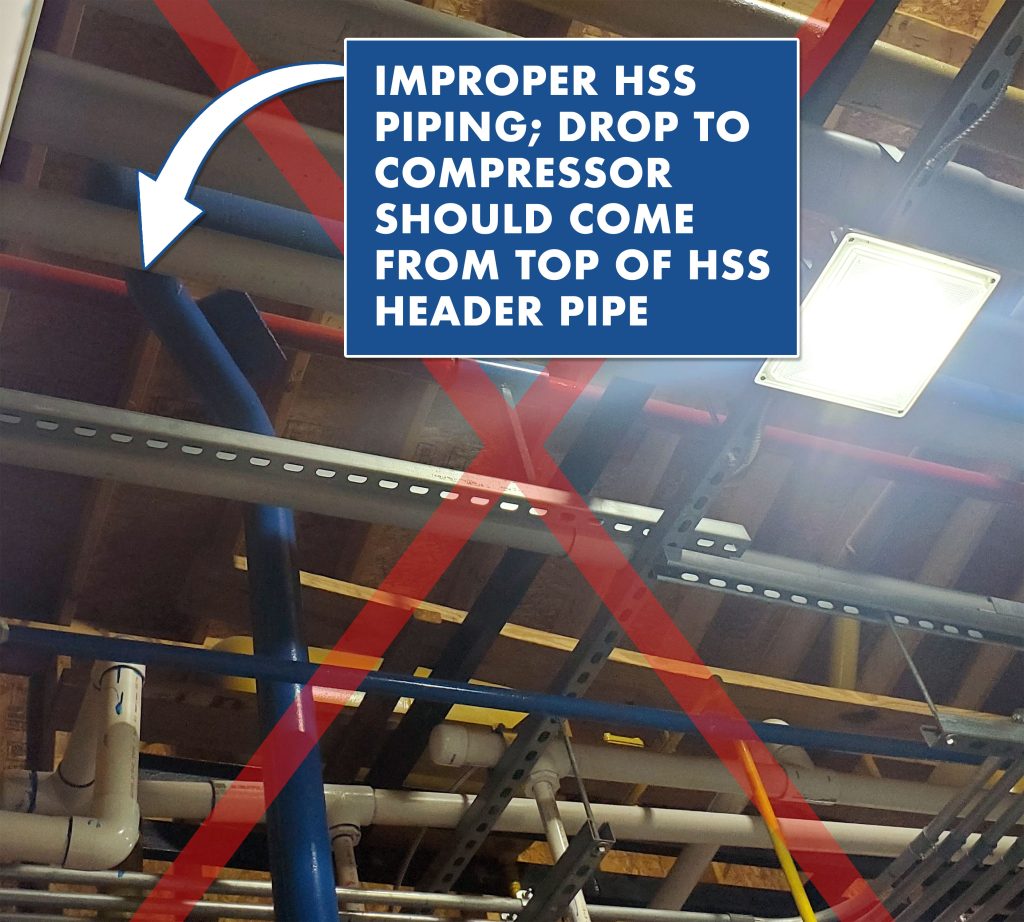
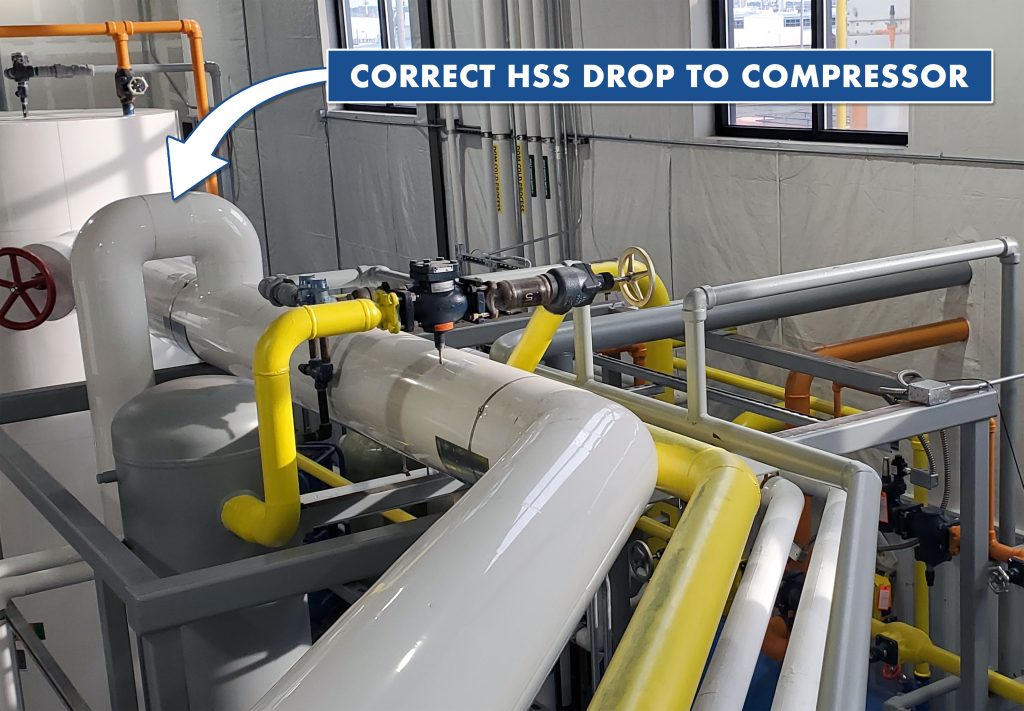
Solenoid Valve Beacon Lights
Simple improvements like adding solenoid valve beacon lights are cheap yet effective. These lights indicate when a solenoid valve is energized, aiding in system monitoring and troubleshooting. This minor upgrade can improve operational visibility and reduce the time spent diagnosing issues.
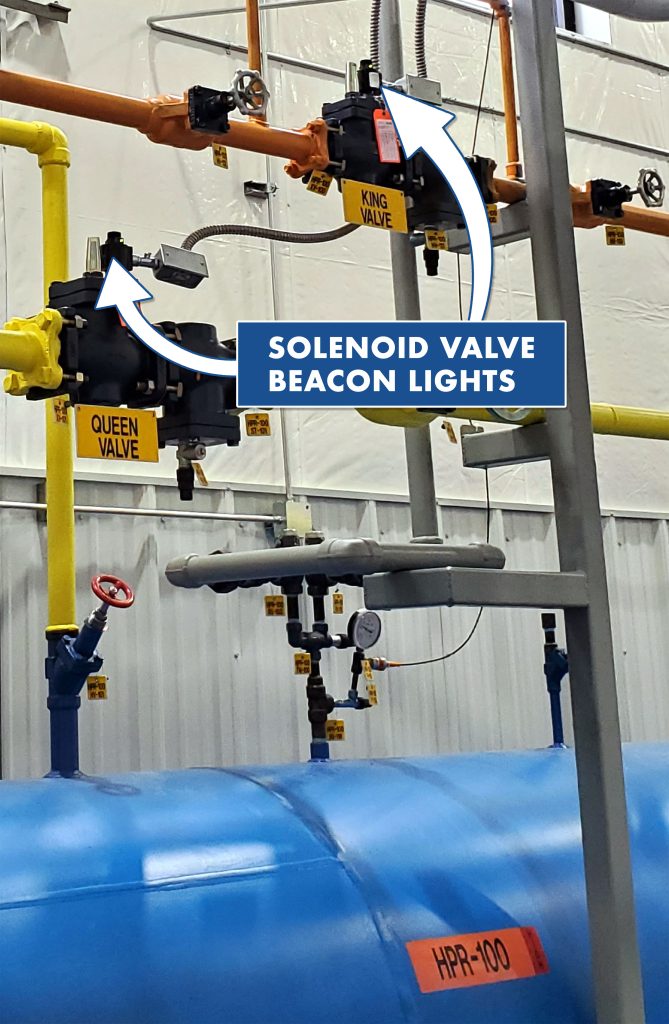
Ammonia Detection and Ventilation Systems
Ammonia detection and ventilation systems are critical components to meeting code and keeping employees safe. Please see AIS article Ammonia Detection and Ventilation for more information.
Glycol Compressor Cooling
Adding a glycol cooling system to your compressors is a massive opportunity for water savings. This can significantly reduce the water your plant uses and keep scale from building up in the compressor heads. Please see AIS article Stop Sending Your Money & Water Down The Drain! for more information.
The experts at Automatic ICE™ Systems can help you keep your facility in top form. Reach out to us today!