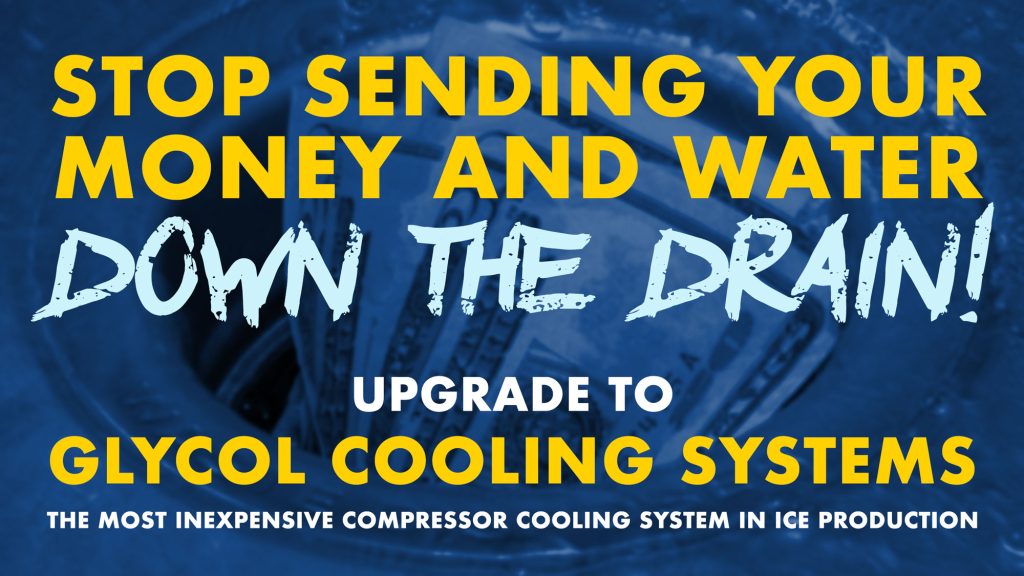
Did you know the average packaged ice plant wastes over 200 gallons of water for every ton of ice produced just for compressor cooling? That is almost 1 ton of cooling water down the drain for every ton of ice in the bag! Did you also know that in many locations it costs more to send that water down the drain than it does to buy it from the City? So, you are paying for it twice!
Every gallon of water you send to your compressors is a gallon that isn’t going to ice production. Many packaged ice plants have trouble with low water supply pressures and flows. Pump cavitation from low water levels causes all sorts of trouble. Having adequate water pressure and flow results in more ice produced per cycle, less chips and fines, and better flushing. All allowing more ice to go in the bag!
Commercial water costs are estimated to rise over 10% in 2022, on average. In some places, rates will be even higher and will continue to rise every year!
WHAT IS COMPRESSOR COOLING?
Compressors generate a lot of heat during the compression cycle. Most of this heat is transferred to the refrigerant and rejected through the system’s condenser. But, some of the heat is transferred to the moving parts of the compressor. Moving parts and high heat do not mix. The compressor cooling circuit removes the heat from the cylinder heads, as well as the oil.
CITY WATER COOLING: THE EXPENSIVE WAY
Historically, ice plants have used city water in a single pass cooling system, where the city water passes through the cooling circuits, then sent down the drain. But, this is expensive, and over time, will buildup scale inside the cooling circuit that is difficult to clean. Many municipalities, cities, and states have codes in place that make city water cooling illegal!
ALTERNATIVE COOLING METHODS
Plants have also tried to cool compressors by pumping condenser water from the condenser sump to the compressors and back; This is a bad idea! Condensers evaporate hundreds, if not thousands, of gallons of water every day, leaving behind all of its minerals. This is called CYCLING UP, and if this water is used for cooling compressor circuits, it will cause scale buildup, clogging, and worst of all, corrosion. If a cooling circuit gets blocked or heat becomes non-uniform across the cylinder heads, the compressor can FAIL.
Ammonia DX (Direct Expansion) cooling has also been done in the past. This method involves piping High Pressure Liquid Ammonia to the compressor cooling circuit, where it expands into gas and picks up the heat. After passing through the compressor, the gas is then returned into the main suction line. This method is great if you want to conserve water, but terrible if you want to produce ice. The average ice making system will see nearly 5% less ice produced. This is because 5% of your compressor capacity is now going towards the cooling circuit instead of making ice. No good!
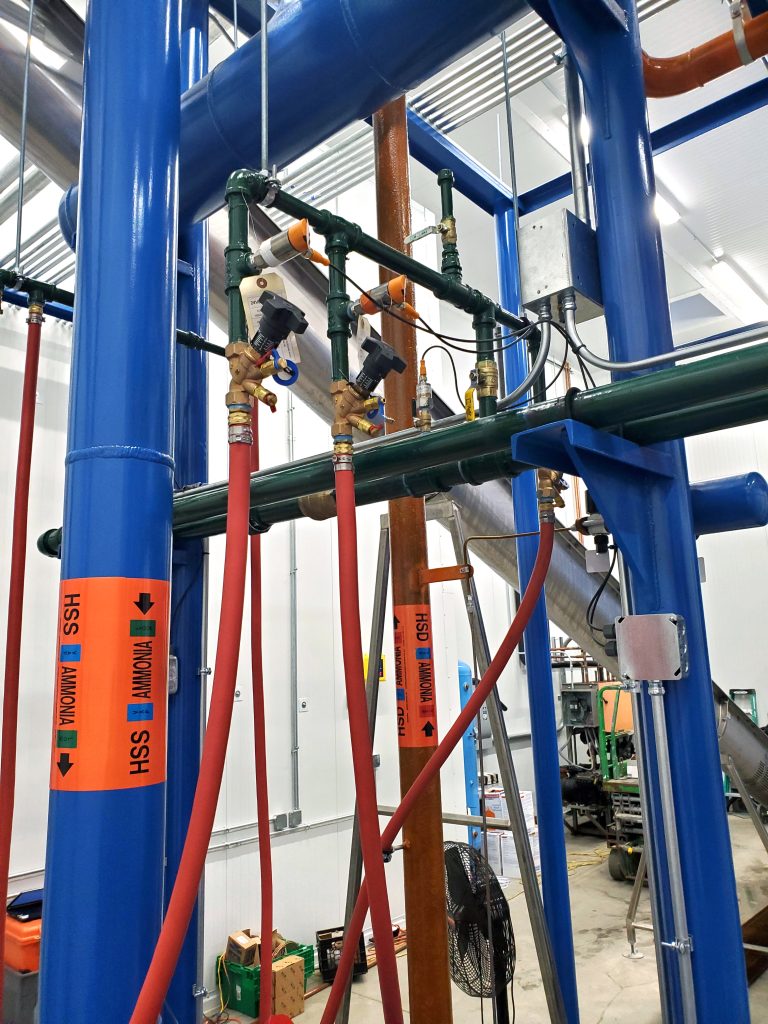
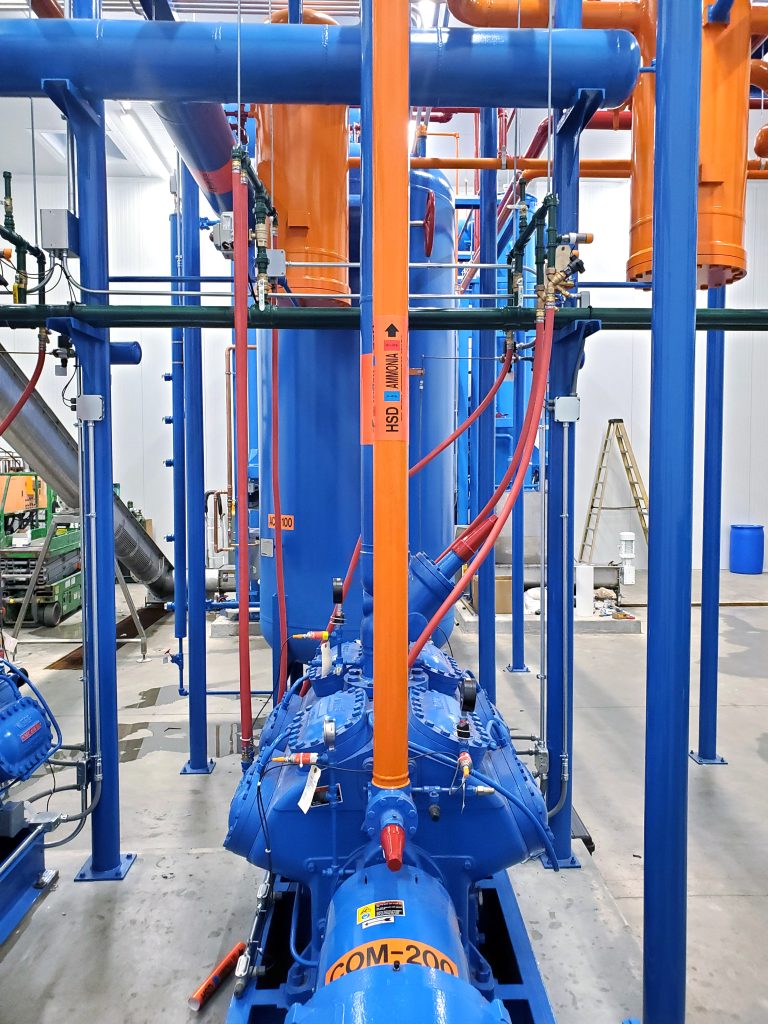
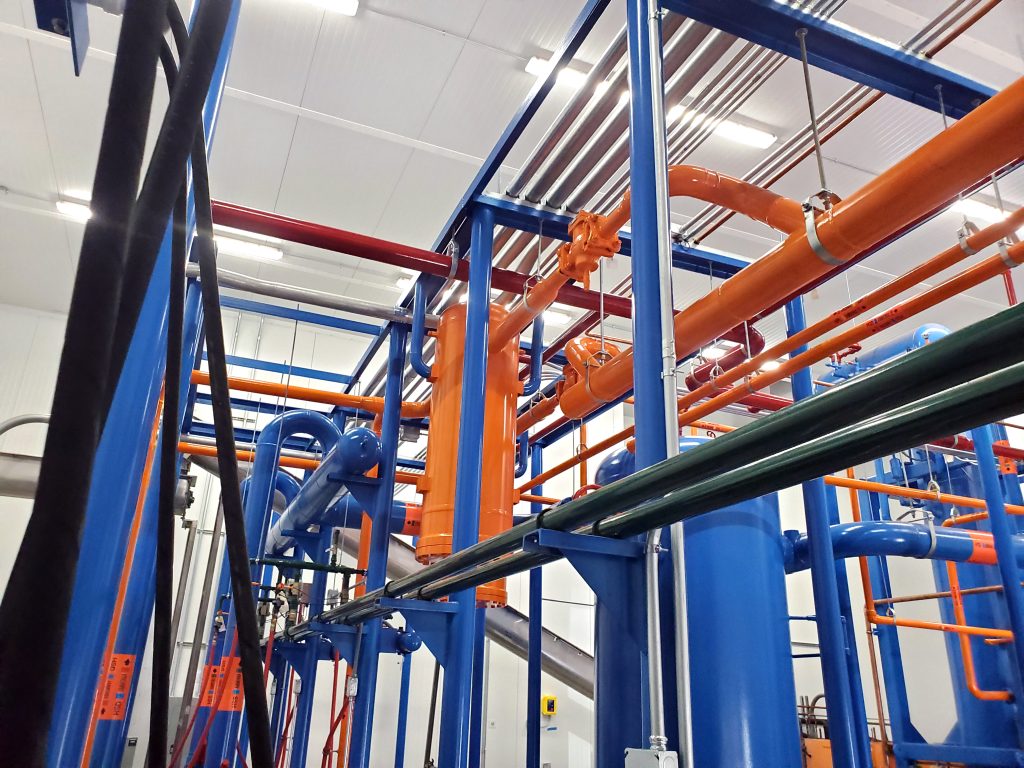
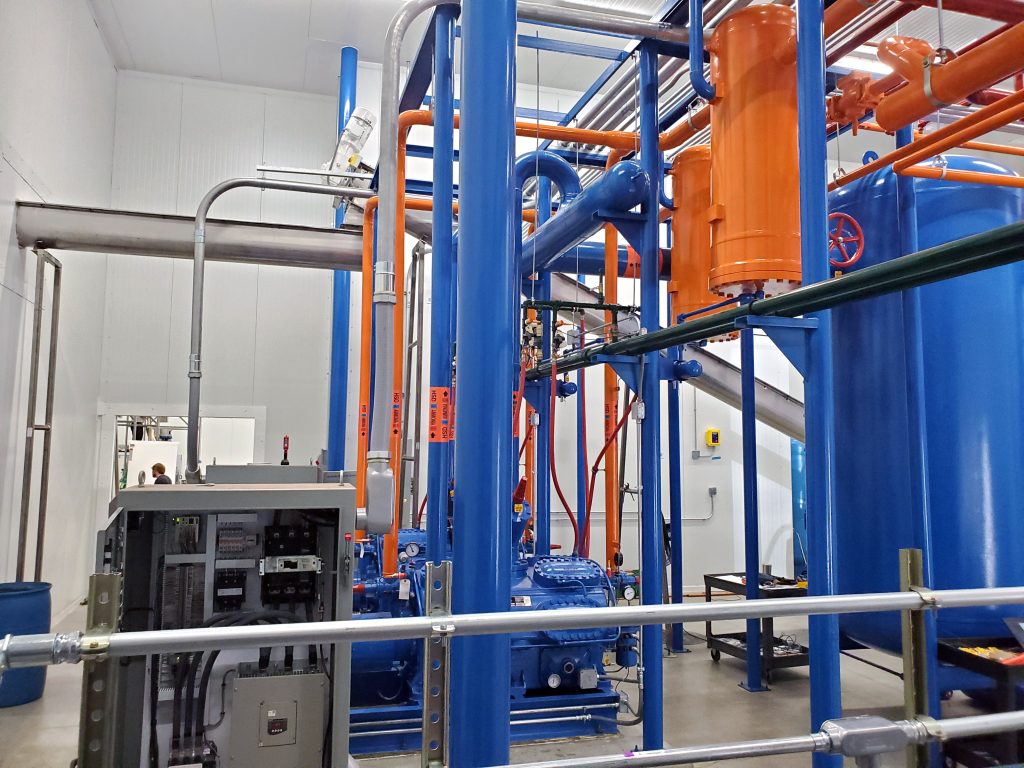
THE BEST METHOD OF COMPRESSOR COOLING:
GLYCOL COOLING SYSTEM
The Glycol Cooling System is the BEST WAY to save water and produce more ice! The AIS Glycol Cooling System is a closed loop circuit that utilizes a special auxiliary coil built into the evaporative condenser. It evaporates water to reject the compressor heat. It is a closed loop system, which means it is completely sealed and pressurized. No air, dirt, or debris is allowed into the system, keeping it clean and long lasting. Glycol is like antifreeze; It prevents corrosion and doesn’t freeze.
Lower water and sewer bills! This system uses less than 2% of the water that a city water cooled system does. That is more money in your pocket and more ice in the bag!
The operating costs of this system includes electricity for a small 2.5HP – 5HP pump, and around 3.5 gallons of water per ton of ice produced.
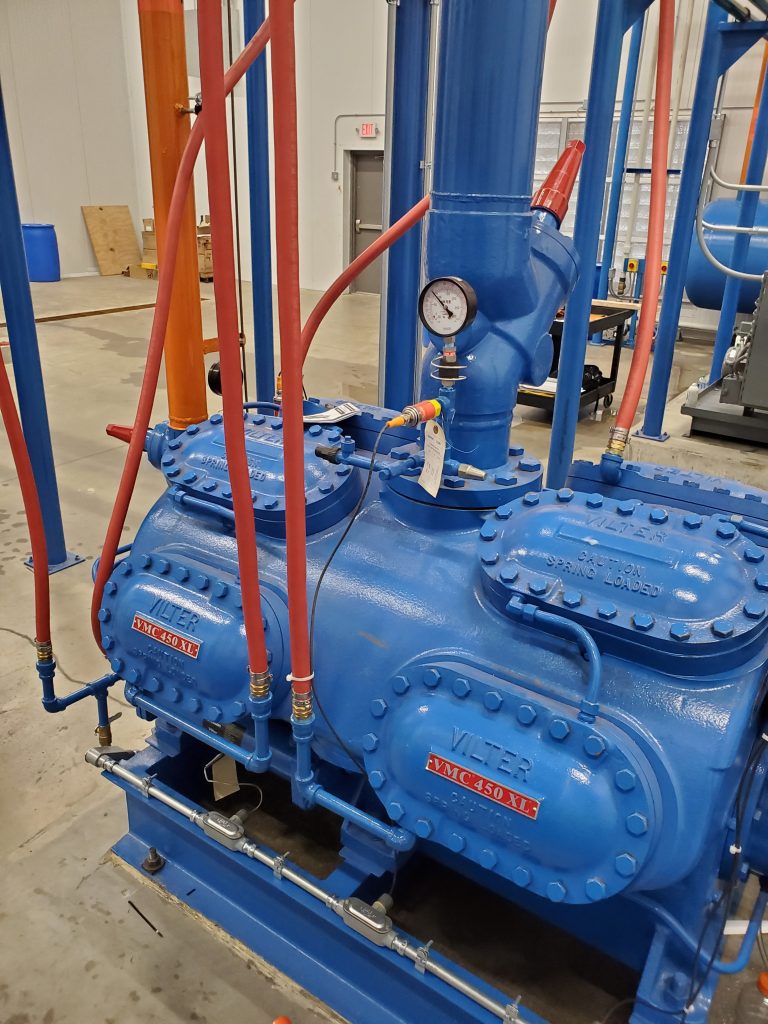
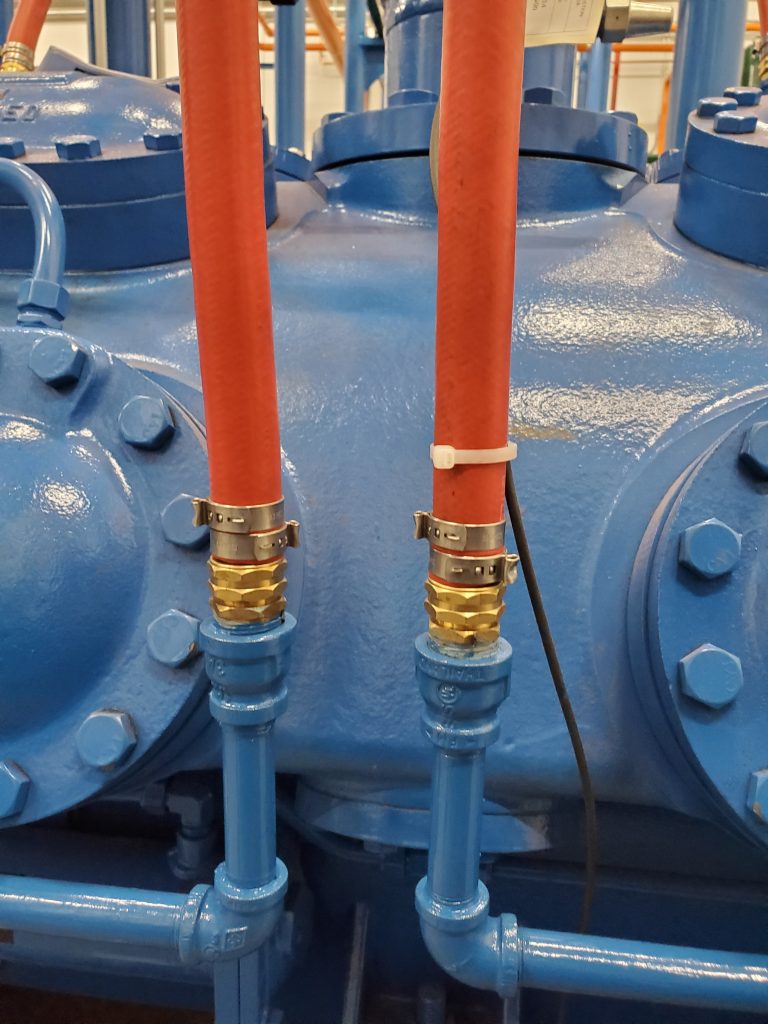
HOW TO GET A GLYCOL COOLING SYSTEM?
The Glycol Cooling System relies on the auxiliary circuit in the evaporative condenser. This circuit is very cheap and easy to add to new condensers at the time of the order. It cannot be added to existing condensers without replacing the entire coil pack, which costs almost as much as a brand-new condenser.
The best time to add a Glycol Cooling System is during a plant expansion when more ice making capacity is being added. Because a new condenser must be included during this expansion, the glycol circuit can be added at very little cost. In addition, the controls integration for the Glycol Cooling System can be included in the project engineering.
Alternatively, if a plant expansion is not planned, a condenser replacement can be done at any time. Typically, a condenser has a useful life of 20+ years, if maintained properly. If an existing condenser is at the end of its useful life cycle, then it can be a great opportunity to investigate a replacement. Not only can a glycol cooling circuit be added to a new condenser, but also new condensers are inherently more energy and water efficient than 20-year-old models, leading to even more operational savings year after year. Controls integration will have to be considered during this time to ensure existing systems have the capability to control the Glycol Cooling System. A standalone control system can also be added when existing control systems cannot be used.
If you would like to learn more about upgrading your facility’s cooling systems by converting to glycol, please contact an AIS Regional Manager or talk to one of our Customer Care Team members.